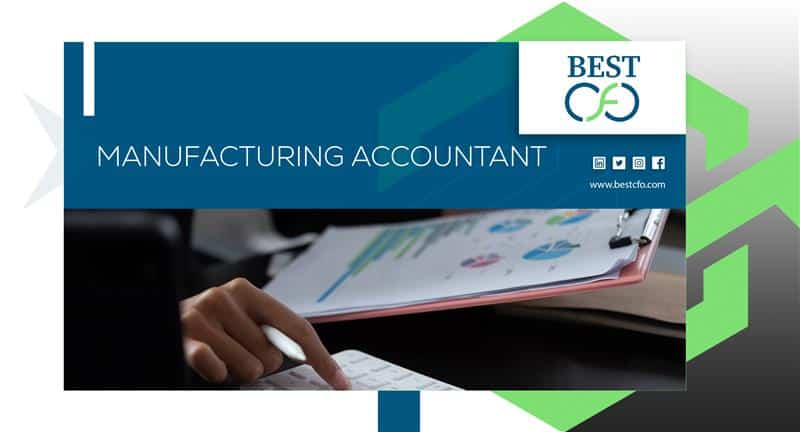
Getting your Trinity Audio player ready...
|
How A Manufacturing Accountant Can Boost Your Bottom Line
Running a manufacturing business comes with a unique set of financial challenges. Between keeping production costs low, managing inventory efficiently, and staying compliant with tax regulations, it can feel like a never-ending balancing act. That’s where a manufacturing accountant steps in — a professional who doesn’t just crunch numbers but helps boost your bottom line through smart strategies and deep industry knowledge.
In this blog, we’ll walk you through how an accountant in manufacturing supports business growth, improves cash flow, and ensures financial accuracy — all while keeping things simple and practical. Whether you’re a small business or part of a large corporation, this guide is packed with tips you can actually use.
Let’s dive into the key ways a manufacturing accountant can strengthen your company’s finances.
Understanding the Role of a Manufacturing Accountant
A manufacturing accountant is not your everyday bookkeeper. While general accountants work across various industries, an accountant in manufacturing specializes in the production and manufacturing space. This field requires a different approach because of the complex processes and detailed cost tracking involved.
They don’t just manage expenses — they analyze every part of the manufacturing process. From raw material usage to finished product sales, they track the cost of goods sold (COGS), overhead, and gross margin — all crucial numbers for decision-making.
Key Financial Metrics to Monitor
Here are some metrics that a manufacturing accountant regularly tracks:
- COGS: Helps determine how much it costs to produce goods.
- Overhead costs: Indirect expenses like utilities, labor, and rent.
- Gross margin: Shows how much profit your business is making before other costs are deducted.
By keeping an eye on these numbers, they provide feedback that helps your business stay lean, agile, and profitable.
Key Responsibilities of a Manufacturing Accountant in the Industry
An accountant in manufacturing wears many hats. Let’s break down what they actually do day to day:
Cost Accounting and Job Costing
They track every dollar spent on production. With cost accounting, they calculate the true cost of making each item. Job costing helps assign costs to specific orders or projects, especially important in custom manufacturing.
Inventory Management and Valuation
Inventory is cash sitting on your shelves. An accountant in manufacturing helps you manage it wisely, avoiding overstocking or shortages, while accurately valuing it for accounting and tax purposes.
Financial Reporting with KPIs
These accountants create reports based on manufacturing-specific KPIs (Key Performance Indicators), not just generic corporate finance metrics. This allows for smarter decisions that match your business operations.
Regulatory Compliance
They help you follow industry regulations, avoiding penalties or audit problems. Their knowledge of business ethics, policy, and accounting standards ensures you’re always compliant.
How a Manufacturing Accountant Improves Profitability
Your bottom line isn’t just about sales — it’s about controlling costs, improving margins, and planning ahead. Let’s look at how an accountant in manufacturing can help make that happen.
Cost Control and Reduction Strategies
An accountant in manufacturing dives deep into your operations to find hidden costs that eat into profits. They also analyze overhead and offer lean accounting solutions — cutting waste without sacrificing quality.
Optimizing Pricing Strategies
Many companies guess their prices — big mistake. An accountant in manufacturing calculates true product costs using accurate data. This ensures you’re pricing to cover costs and generate strong profit margins, while staying competitive in your industry.
Better Cash Flow Management
Cash is the fuel of your business. An accountant in manufacturing improves how you handle accounts payable and receivable, keeps inventory levels just right, and boosts working capital — which means more money in your pocket when you need it most.
Tax Planning and Compliance
They identify manufacturing-specific tax deductions, such as R&D credits, which many businesses overlook. They also help with tax compliance — saving you from costly mistakes and surprises during audits.
Financial Forecasting and Budgeting
Forecasting helps you prepare for ups and downs in demand. An accountant in manufacturing builds realistic budgets, runs “what-if” scenarios, and helps plan big purchases like new equipment, based on your growth goals.
Advanced Strategies a Manufacturing Accountant Can Implement
Beyond daily tasks, a skilled accountant can introduce advanced tools that take your business management to the next level.
Activity-Based Costing (ABC)
ABC is a smarter way to assign costs. Instead of using broad estimates, it tracks the real activities driving expenses. This approach gives a clearer picture of which product lines are actually making money — a must-have for strategic decision-making.
ERP and Accounting Software Integration
Using tools like QuickBooks Manufacturing, SAP, or Oracle, an accountant in manufacturing can connect your accounting with your production processes. This reduces human error, saves time, and makes your data more useful. With the right accounting software, you’ll get real-time insights to guide your next move.
Break-Even Analysis and Profitability Modeling
Want to know when your business will start making a profit? A manufacturing accountant runs break-even analysis to find out. They also model different production scenarios to see which products bring in the most money — useful for scaling your operations or launching something new.
Risk Management and Financial Audits
Every business has risks — from fraud to financial missteps. Your manufacturing accountant helps set up controls to catch problems early and makes sure you’re ready for audits with clean, accurate records. This builds trust with banks, investors, and partners.
Choosing the Right Accountant for Your Manufacturing Business
Not all accountants are the same. Here’s what to look for when hiring one for your manufacturing company:
Qualifications Matter
A good accountant in manufacturing should have a bachelor’s degree in accounting or finance, along with certifications like CMA (Certified Management Accountant). Experience in the manufacturing world is a big plus.
Smart Questions to Ask
- Have you worked with manufacturers before?
- Are you familiar with our industry-specific software?
- How do you help improve cash flow and reduce waste?
These questions test their real-world consulting skills and their understanding of your needs.
In-House vs. Outsourced Accounting
Hiring in-house gives you someone who knows your organization inside and out, while outsourcing can give you access to expert consultants without long-term employment costs. Think about your size, budget, and goals before deciding.
Conclusion
If you’re serious about growing your manufacturing business, investing in a manufacturing accountant is a smart move. They help you control costs, improve profit margins, stay compliant, and plan for the future.
Whether you’re part of a small team or a larger enterprise, their knowledge can drive real progress. And if you’re ready to go even further, consider partnering with a Best CFO service that offers both strategic vision and day-to-day financial leadership.
In today’s fast-moving economy, having the right numbers — and the right person managing them — makes all the difference.
FAQs
What’s the difference between a Manufacturing Accountant and a general accountant?
An accountant focuses on tracking and analyzing production-related costs, while a general accountant works with broader financial data that may not cover the complexities of the manufacturing sector.
How can an accountant in manufacturing help my small business?
Even if you’re a small business, they can help you manage inventory, improve cash flow, reduce waste, and stay compliant with tax rules — giving you a competitive edge.
Is accounting software necessary for manufacturers?
Absolutely. Tools like QuickBooks Manufacturing or SAP help automate tasks and improve accuracy. A manufacturing accountant ensures the software is set up properly for your unique needs.
Can they help with international trade and taxes?
Yes. A good accountant in manufacturing understands import/export regulations and can help with cross-border tax planning and compliance.
Should I hire in-house or use an outsourced CFO service?
It depends on your budget and the complexity of your operations. For growing businesses, an outsourced Best CFO service might offer both flexibility and expertise at a lower cost.
-
Previous Post
The 13-Week Cash Flow Model Every Business Needs
-
Next Post
What Are the 5 Sources of Funding?
Post a comment Cancel reply
Related Posts
Accounting as a Service: How Accounting Firms Deliver More Value
What Are the 5 Sources of Funding? So, you’ve got the dream. The vision. The…
501(c)(3) vs 501(c)(4): What’s The Difference?
What Are the 5 Sources of Funding? So, you’ve got the dream. The vision. The…
Top 5 Benefits of Hiring a Virtual Controller for Your Business
How to Improve Your Bad Debt to Equity Ratio: A Complete Guide If you’ve ever…
Understanding the DCAA Chart of Accounts: A Complete Guide
How to Improve Your Bad Debt to Equity Ratio: A Complete Guide If you’ve ever…